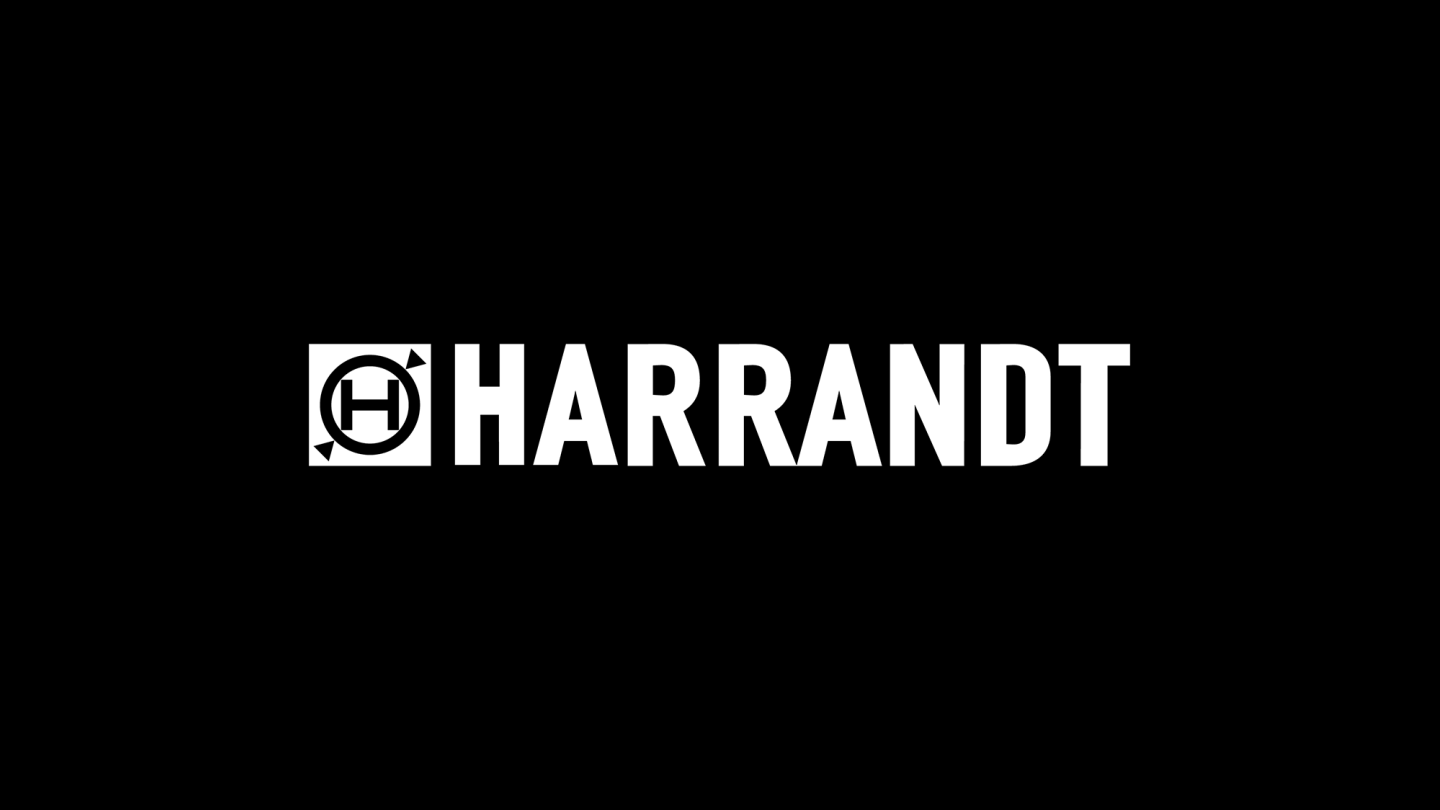
Quality optimization made
in Germany - for automa-
ted processes with the
highest precision
requirements.
Assembly, Testing &
Measuring. Automated.
Our goal is to improve our customers' products and processes. Continuously. Sustainably. Reliably.
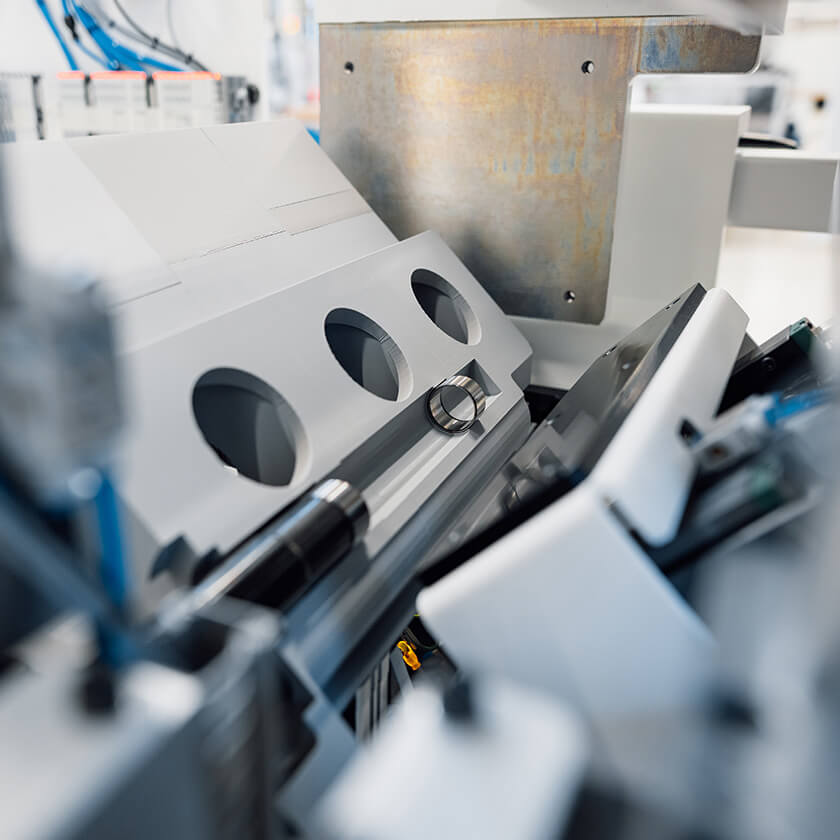
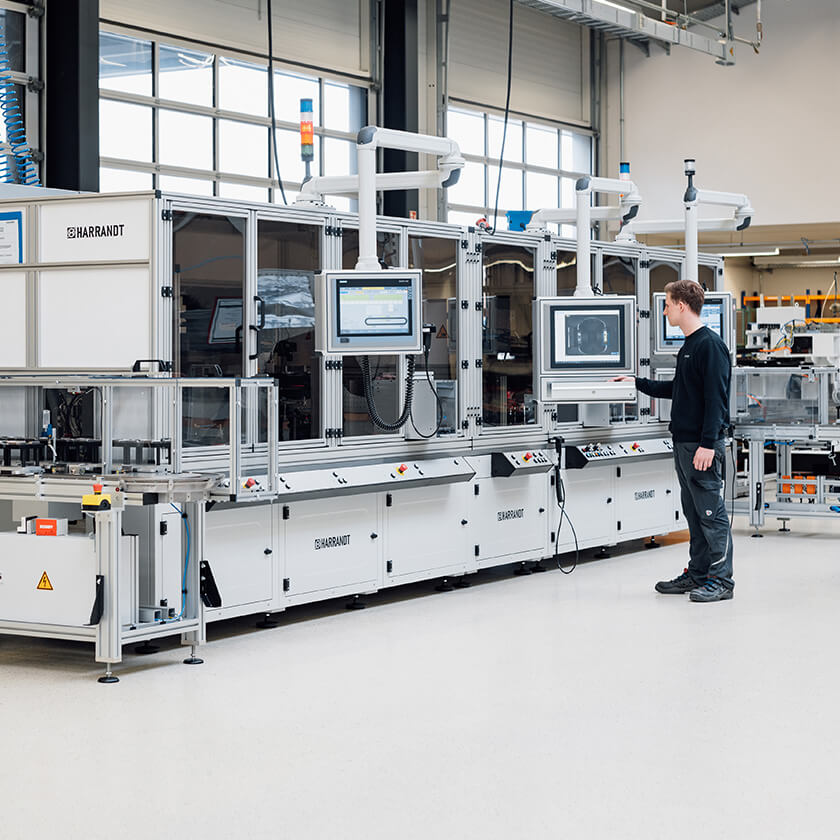
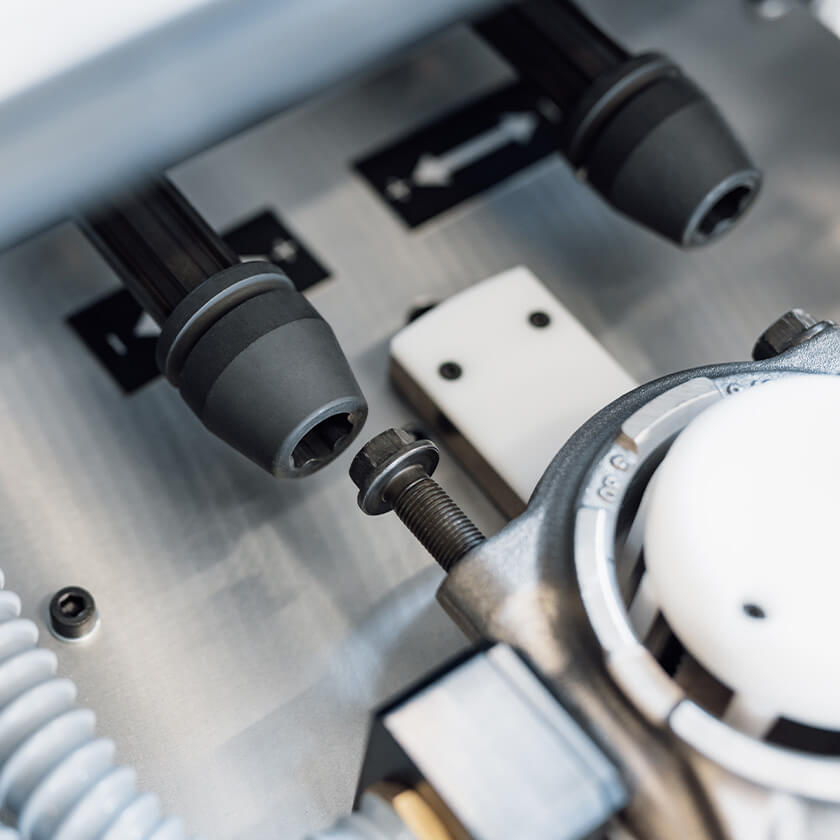
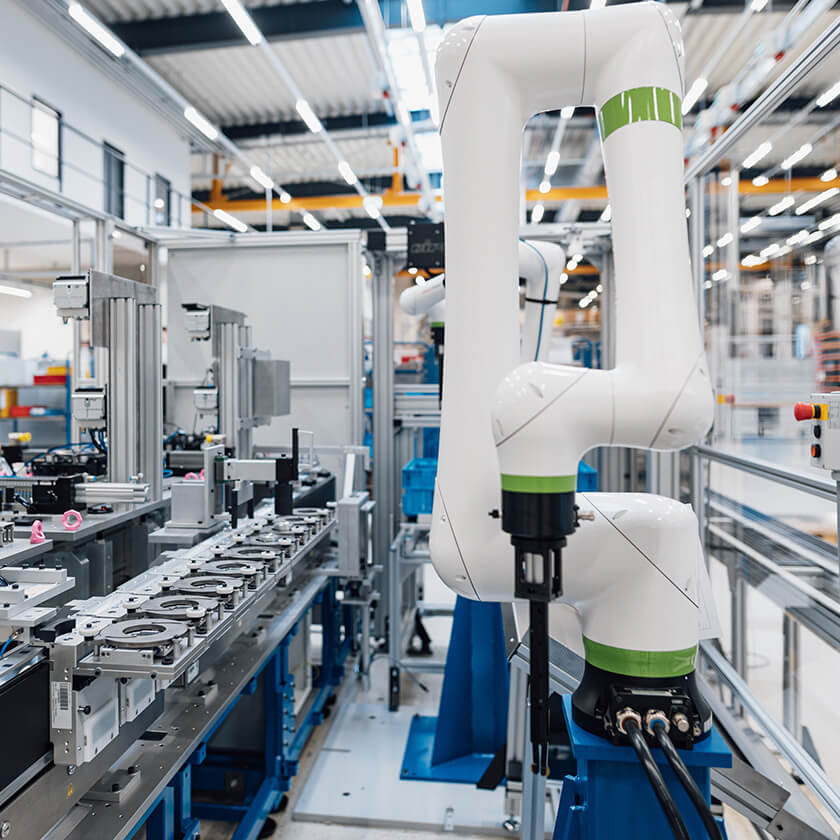
Quality-optimized production processes in step with the times.
For 60 years our brand Harrandt has been synonymous with the highest precision and accuracy, a high level of in-house manufacturing and development expertise and intelligent solutions. Whatever goal you set: With our tailor-made, intelligent and automated measuring and testing systems, we implement your ideas precisely, future-proof and always focused on your specific needs. Combined with our contactless assembly and joining processes they ensure highest quality and productivity standards.
years of quality
over 30 countries
ment to 1 μm
You have high quality requirements.
We meet them.
Solutions from Harrandt combine everything you need to improve your upstream and downstream production processes: from software development to mechanical and electrical engineering to implementation of the entire measurement, testing and assembly technology - all critical competences are in-house. Our highly specialized manufacturing competence enables us to develop individual solutions for you quickly and in a highly flexible manner.
Profound understanding of processes across multiple industries.
As the world market leader in measuring, testing and assembly technology for automotive pistons Harrandt is constantly advancing its competence in digitalising factory automation processes. Traceability, process data analysis with integrated feedback loop – it is our mission to make your manufacturing and quality processes even more efficient, precise and future-proof. Across multiple industries, we set standards with our thorough understanding of products, processes and technologies. Thanks to our expertise, we meet your requirements with innovative results - providing you with real added value and enabling you to keep your promise of quality and expand your lead as a premium manufacturer.
Create your own impression.
- #industry40
- #qualityassurance
- #innovation
- #smartfactory
- #emobility
- #optimization
- #automotive
- #challenge
- #robotics
- #machinelearning
- #IoT
- #team
- #events
- #cobot
💡 We won't leave you in the dark! 💡
Precision, efficiency and quality are crucial in modern manufacturing. This is exactly where we come in from: Automated measuring, testing and assembly modules from Harrandt ensure reliable processes and the highest product quality - individually tailored to your requirements.
🔍 Measuring accuracy at highest level
🛠 Precise and efficient assembly processes
✅ Seamless quality assurance thanks intelligent testing technology
What makes us special? A holistic process understanding. We not only consider individual work steps, we consider the entire value chain.
Our focus is on understanding your specific customer needs and developing solutions that can be perfectly integrated into your production processes
From electromobility to the automotive industry and other high-precision sectors - our technologies help you to produce faster, more efficiently and more sustainably.
Future-proof solutions for your production! Let's set new standards together.
Please contact us via our contact form.
- #industry40
- #qualityassurance
- #innovation
- #smartfactory
- #emobility
- #optimization
- #automotive
- #challenge
- #robotics
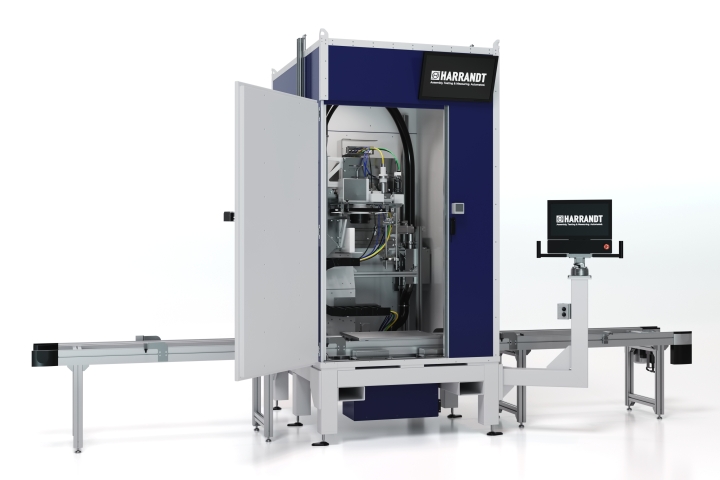
HARRANDT presents pioneering product innovation in the sector of e-mobility: laser welding cell
We are pleased to announce the launch of our latest product innovation: the laser welding cell for the e-mobility sector.
This pioneering solution marks a milestone in our ongoing effort to provide innovative technologies for the automotive industry.
HARRANDT's laser welding cell offers a first-class solution specially for the stator production of electric engines by enabling highly precise, efficient welded joints and all independent of manufacturer. This technology not only improves production processes, but also increases the quality and reliability of the engines produced.
We are glad to invite you to learn more about our laser welding cell and further innovative solutions from HARRANDT.
Contact our sales team for more information or visit us at Coiltech Augsburg booth 1-E29.
your HARRANDT-Team
- #industry40
- #qualityassurance
- #innovation
- #smartfactory
- #emobility
- #optimization
- #automotive
Fully automated assembly line
Our fully automated assembly line is the perfect solution for efficient and precise assembly, as well as inspection and measurement of small and micro parts.
Equipped with the latest robotic technology, an integrated camera system from VISIO NERF to detect the gripping points of the loading robot and a well thought-out SuperTrak conveyor.
Specially made workpiece carriers, which are fixed to the conveyor, thus enable the transport to the individual assembly and measuring stations.
The integrated robots handle the loading and unloading of parts to and of the assembly line and can be quickly adapted to different requirements.
Our automated assembly and measuring stations are user-friendly and easy to operate. On the one hand, they enable the assembling of a wide variety of small and very small parts, and on the other hand, they can be used to monitor quality characteristics.
The stations can be individually adapted to your needs so that the quality of your products is guaranteed at all times.
Use our profound knowledge to your advantage.
- #industry40
- #qualityassurance
- #innovation
- #smartfactory
- #team
- #optimization
- #automotive
- #robotics
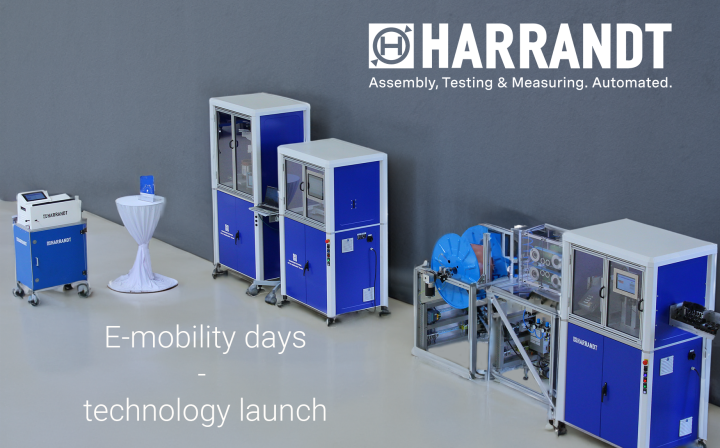
HARRANDT technology launch
Are you a wire manufacturer, stator producer or line builder in the field of e-mobility and you are looking for the right test and measurement technology?
Benefit from our exclusive technology launch and secure one of our limited appointments today.
Contact us by phone on +49 7195 90680 0 or send us an e-mail to sales@harrandt.com.
We look forward to get in touch with you and to welcome you in our company.
- #qualityassurance
- #innovation
- #emobility
- #team
- #optimization
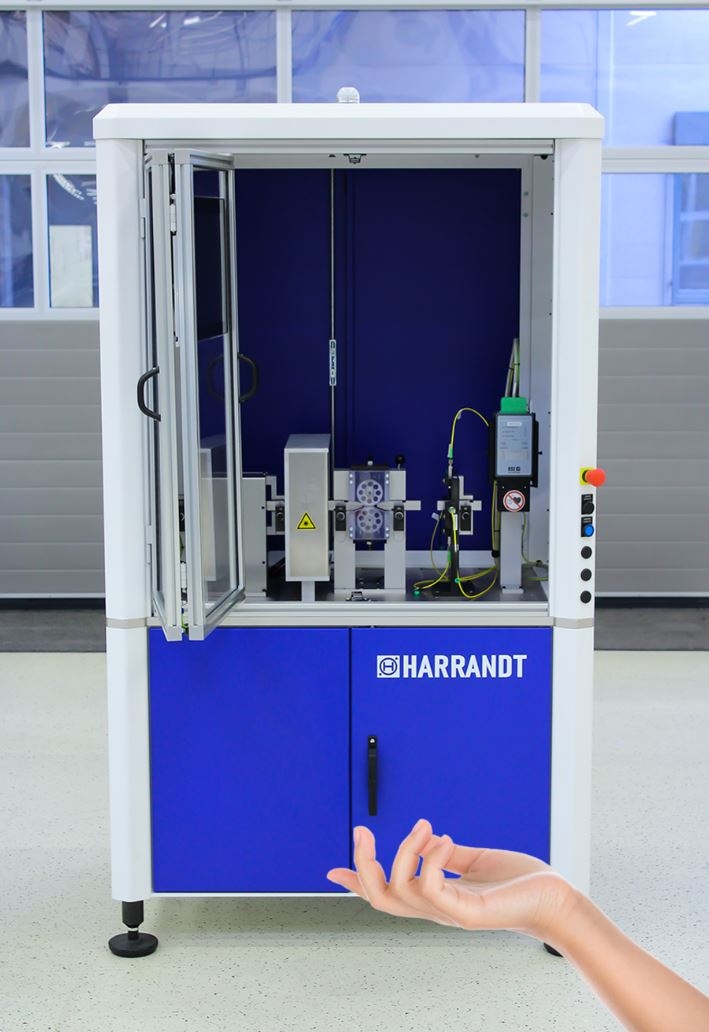
Increase your quality reliable with the use of our wire testing module
We are proud to present you our wire testing module. With the successful acceptance we are able to hand over our wire testing module into customer hands. To respond to special and individual wishes and to offer the perfect solutions for the challenges of our customers is a matter close to our heart. Would you like to learn more about the functions and the added value you can gain by using our E-Mobility modules?
Solution concepts from Harrandt combine everything you need to optimize your upstream and downstream production processes: from software development
through mechanical and electrical design to the implementation of the complete measurement, testing and assembly technology - all from a single source.
Process-safe, powerful and efficient.
Contact us by phone under +49 7195 90680 0 or simply send us an e-mail to sales@harrandt.com.
We look forward to getting in touch with you.
- #qualityassurance
- #innovation
- #emobility
- #team
- #optimization
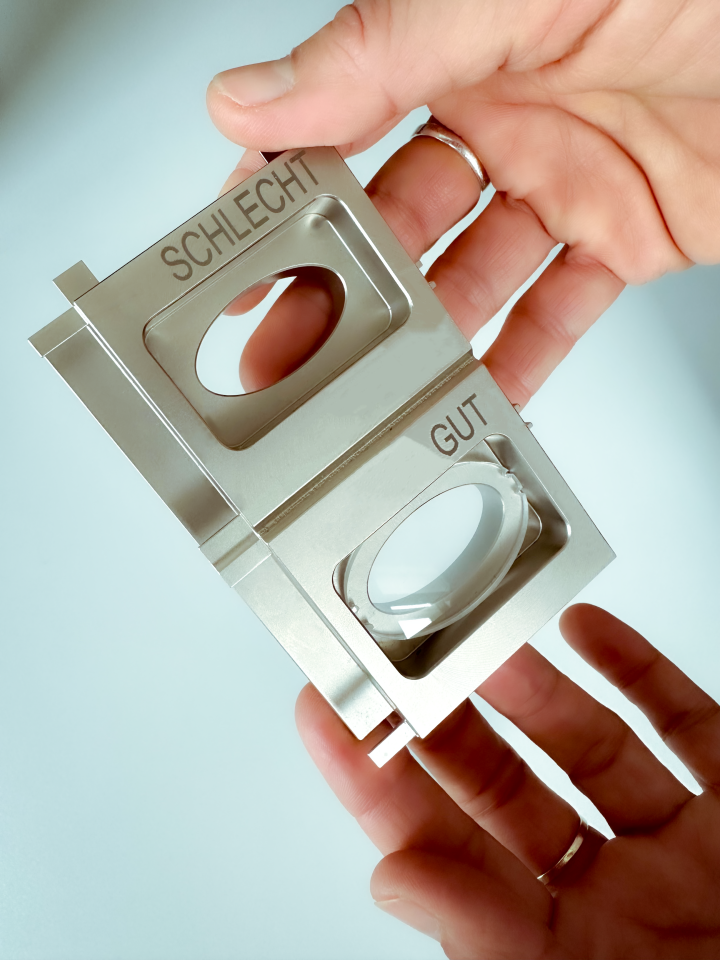
"Life is magical, you just have to see it through the right glasses"
More than 950 million people worldwide suffer from correctable refractive errors. They would need glasses but can't afford them or don't have access to optical care at all. The consequences: Children can't learn well, adults can't hold skilled jobs or even work at all, and they can't feed their families. The resulting global income loss is more than $269 billion annually, according to a 2019 WHO study.
Since its founding in 2012, OneDollarGlasses has been dedicated to solving this problem: Starting with the construction of a simple bending machine for eyeglass frames by founder Martin Aufmuth, the association has grown to more than 280 employees in currently 10 program countries, 35 permanent employees and a large number of volunteers in Germany, who pursue the goal of providing basic optical care for all people worldwide. In addition to the supply of glasses, eye tests and the training of local and training of local staff, as well as educational work and international networking with partners.
Today, the glasses are produced in Africa, Latin America and Asia and the quality standard, must be the same everywhere and, above all, consistent. In order to maintain this quality standard the lenses have to be subjected to random checks within the production and supply chain before the lenses are sent to the project countries.
The material cost of one glasses is around one US dollar, which explains the name of the association. The frame of the glasses is made of a flexible spring steel wire and colorful pearls round off a stylish design. By means of bending machines, glasses of different sizes can be produced. Through a simple modular system plastic lens in strengths from -10.0 to +8.0 diopters can be clicked into the frame with only one hand movement.
Harrandt employee Markus Wöhrbach, deputy head of the development department, became aware of OneDollarGlasses association through a flyer and didn't hesitate for long to get in touch with them. "With such a magnificent project, Harrandt has to be able to contribute his expertise in positive form," Markus said.
Last December, we welcomed Dr. Uwe Schüller and Udo Ulrich, both bending trainers and machine coordinators from OneDollarGlasses at our company. In addition to getting to meet each other personally for the first time, the "how" was the main focus for us. How can we support OneDollarGlasses positively, sustainably and reliably?
During the conversation, it became clear that precision requirements in the hundredths of a millimeter range are placed on the frame and the lenses. With his in-depth technical understanding, Valery Andreas, production manager at Harrandt, was able to demonstrate the possibilities of machining in order to produce so-called lens gauges. Also Dr. Uwe Schüller and Udo Ulrich believed "that the high accuracy requirements in particular can be achieved by Harrandt." Away from the measuring lens testing process, towards teaching testing. With the help of the lens gauges manufactured by Harrandt, time-consuming and error-prone measuring tests can now be replaced. After sending the first manufactured lens gauge sample to OneDollarGlasses, it didn't take long time for reorder of 6 more lens gauges. Since special focus is placed on the manufacturing tolerances for compliance with the quality standards, the lens gauges were 3D measured and recorded. After the measurement results were available, René Freiherr von Künßberg, Head of Optics, Production and Logistics at OneDollarGlasses, said, "all tolerances were met with considerable precision in production, so we can use the gauges for quality assurance."
We are particularly pleased not least with the positive response to the lens gauges, but rather with the perception of Dr. Uwe Schüller and Udo Ulrich, that Harrandt shows deep interest in the work and the product of the association OneDollarGlasses and thereby the long-lasting positive effect in the area of social as well as societal activities of the association wants to support. For the future there is already the perspective of further cooperation. We would like to take this opportunity to thank the OneDollarGlasses association for the trust they have given us as Harrandt.
- #qualityassurance
- #innovation
- #team
- #challenge
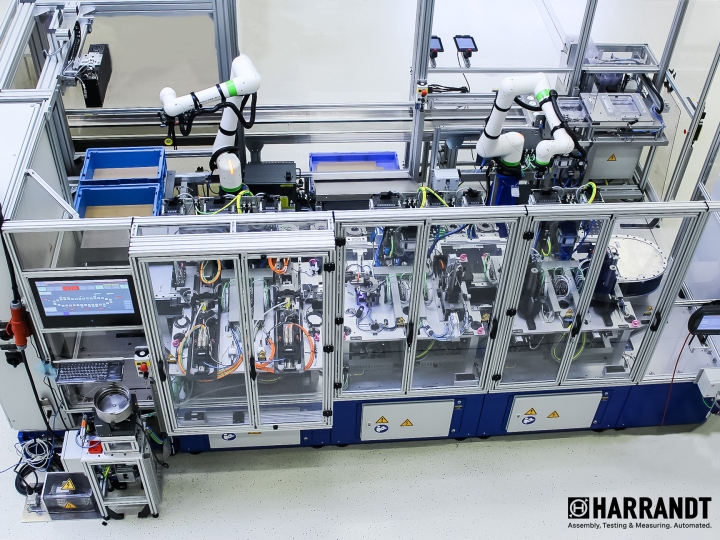
New applications in Harrandt-lines
The most beautiful gift for us and our customers are positive pre-acceptances. All the efforts are coming to an end and the anticipation of our customers is immeasurable to have their ordered machine line in the factory on site. With the installation of the line by our employees, a training, as well as a positive final acceptance, we pass the line into the hands of our customers. We show you here a line, which is initiated by a robot loading. To make sure that the robot knows where to pick up parts, we decided to use a camera system from VISIO NERF for the first time. In specially developed and machined workpiece carriers, the parts to be inspected and assembled pass through the individual measuring and assembly stations via an SuperTrak conveyor. Finally, the assembled and inspected parts are unloaded by a second robot and placed in different carriers as O.K. or N.O.K. according to the inspection results. We wish our customer a lot of pleasure and work simplification with the new line.
- #qualityassurance
- #innovation
- #team
- #optimization
- #automotive
- #robotics
Quality Inspection in E-Mobility
At HARRANDT, we are successfully transferring our expertise in automated measurement, testing and assembly technologies to the e-mobility sector.
In order to visually present our range of performance for "Quality Inspection in E-Mobility Stator Production", we have developed an animation in cooperation with Kinkahuna.
The aim is to show you the process steps within stator production in which our modules can be used as value-added inline and offline solutions. As an add-on, we offer you a central cloud with all measurement and test results in real time.
Use our profound knowledge for your advantage.
- #qualityassurance
- #innovation
- #emobility
- #team
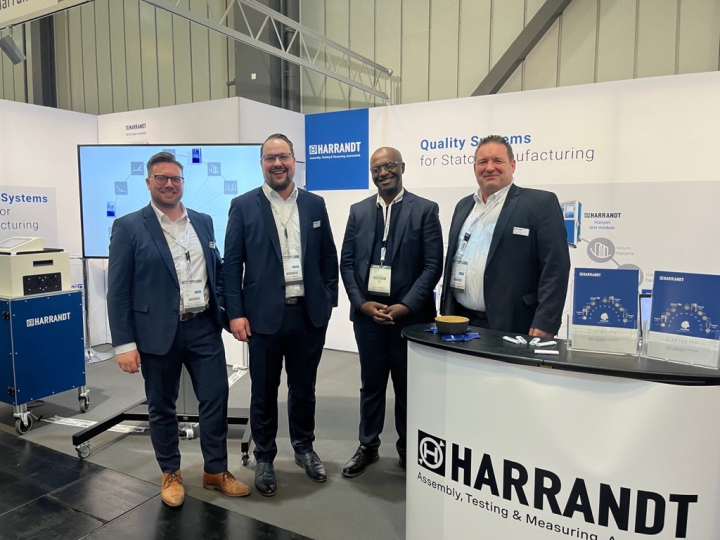
HARRANDT as exhibitor at Coiltech in Augsburg 2023
Also this year HARRANDT was represented as exhibitor at Coiltech in Augsburg on 29.03.2023 and 30.03.2023. Exciting conversations, professional discussions and a common knowledge transfer were in the focus and showed their positive added value.
As a special highlight we were allowed to exhibit our residual material test module. Micrometer precision measurements of the coating adhesion on all four sides of the wire could be demonstrated directly on site. Furthermore, we were allowed to give a speech about "Quality Assurance in Stator Production" at the World Magnetic Conference.
You did not have the opportunity to talk to us personally? We may already inform you that we will exhibit again for you at the Coiltech in Pordenone (Italy) on 20.09.2023 and 21. 09.2023.
- #qualityassurance
- #innovation
- #emobility
- #team
- #automotive
- #events

technologies for intelligent mobility
A big step towards the future - we are very happy to be a member of this great network with stakeholders along the entire value chain. The "Electro Mobility South-West" cluster offers access to current market and industry-related trends. The top cluster "Electro Mobility South-West" is funded by the Federal Ministry of Education and Research and supported by the state of Baden-Wuerttemberg.
- #innovation
- #emobility
- #team
- #automotive

1st REUTLINGEN E-MOBILITY DAYS
Wow, what great reactions and feedback to the 1st REUTLINGEN E-MOBILITY DAYS. Thanks a lot for visiting us and the discussions we had. We're proud that we were part of this live event with such great partners.
- #qualityassurance
- #emobility
- #automotive
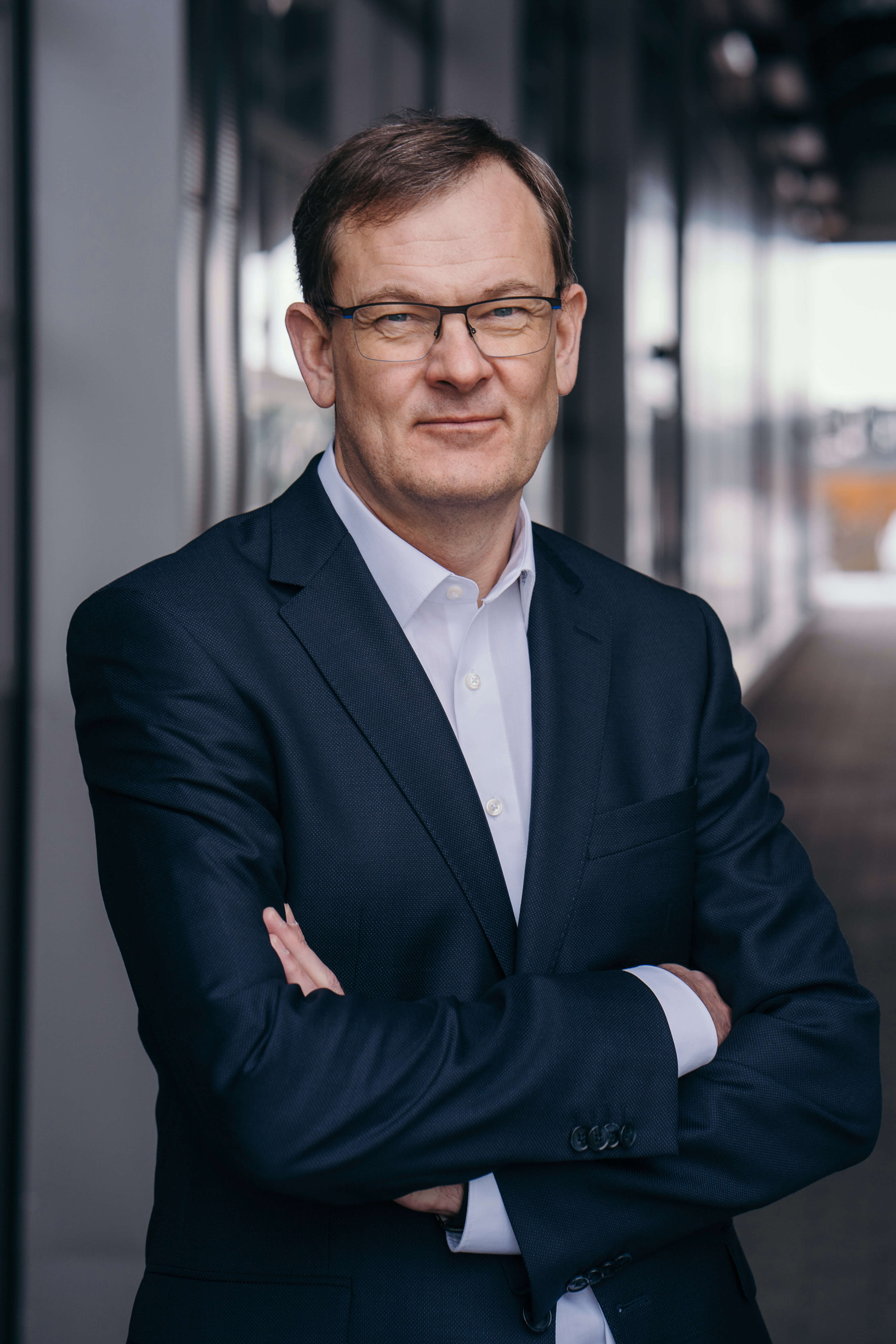
We are pleased to welcome Jan Treede as General Manager Sales and Technology
With more than 20 years of experience in developing business within the Industrial Automation Market, he will be responsible for driving our strategy and to expand the leading position Harrandt holds in High Precision Assembly and Quality Inspection to various new markets such as components for E-Mobility.
- #emobility
- #team
- #challenge
Integrated Hairpin-Stator Inline quality inspection
Our quality solutions for the production of premium hairpin stators can be guaranteed through our master web-based AI (artificial intelligence) database combined with the process control to ensure a high quality of your products. Three inspection modules in production improve quality in the long term and reduce failure costs significantly.
- #industry40
- #qualityassurance
- #innovation
- #smartfactory
- #emobility
- #IoT
- #automotive
In a word: Ralph Höh, Head of Engineering
"With mechanical engineering, we not only want to solve current problems, but also think into the future and deal with possible problems".
- #qualityassurance
- #innovation
- #team
- #optimization
- #automotive
In a word: Jan Maierhöfer
"The advantage for the customer is that the speed and automation of the machines can be increased".
- #industry40
- #innovation
- #smartfactory
- #machinelearning
- #team
- #automotive
In a word: Samy Song, Head of the Innovation and Electronics Department
"Innovation at Harrandt means developing new products based on our years of experience".
- #industry40
- #qualityassurance
- #innovation
- #smartfactory
- #machinelearning
- #emobility
- #team
- #optimization
- #IoT
Harrandt on site.
Feinwerktechnik Otto Harrandt GmbH
Robert-Bosch-Straße 25
71397 Leutenbach-Nellmersbach
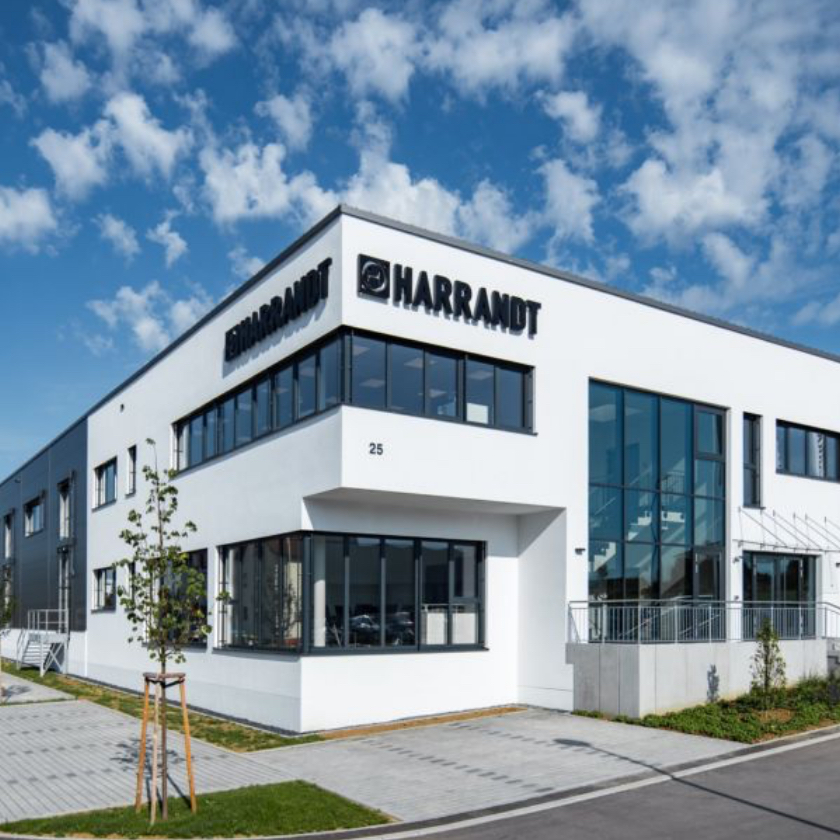